If you’re new to using an air compressor, you may not be familiar with the different components of the system. The same can be said for those who have used a compressor to fill up tires, footballs, rafts, etc. but have never used it with pneumatic tools. For some uses, you can get away with not paying much attention to the two gauges on the compressor. But if you want to get familiar with the compressor and use it properly, it’s good to know why the compressor has two gauges — and what they do.
Your standard compressor has two gauges: the tank gauge and the regulator gauge. Both use pounds per square inch (PSI) as the standard measurement. The tank gauge tells you the pressure inside the tank, whereas the regulator gauge tells you how much pressure the compressor is sending to the tool.
Table of Contents
- What Are the Two Gauges on Your Air Compressor?
- How To Read An Air Compressor Gauge
- How Do Air Compressor Gauges Work?
- How To Adjust an Air Compressor Gauge
- What Do The Gauges Need to Be Set At?
- In Conclusion
- Tank Pressure vs Regulated Pressure FAQ’s
What Are the Two Gauges on Your Air Compressor?
Let’s dive a little deeper into each gauge so you can understand how they work and what they do. This understanding is essential for working properly with air tools and ensuring that your compressor lasts a long time.
Improper use of the gauges can cause premature wear and tear on both the air tools you use and the compressor itself. In some instances, it may prevent you from using certain tools at all, if there’s not enough pressure allowed downstream to the tool in question.
Luckily, it’s easy to understand and read these gauges. To reiterate, these two gauges on your air compressor or the tank gauge and the regulated air gauge.
Let’s start with the tank gauge.
Tank Gauge
The tank gauge on the compressor tells you the pressure inside the tank. The range on the tank gauge will vary depending on the compressor. Compressors used for typical home and DIY projects will have a range of 0 to 150, 0 to 175, or 0 to 200 PSI.
When the compressor’s tank is empty of compressed air, the needle will read at 0. But when the compressor is in use, you’ll be able to watch the needle move as the compressor is used.
When you first turn the compressor on and the pump starts to compress air to fill up the tank, you can watch the pressure on the tank gauge climb to the cut-out point, which can be factory-set at anywhere between 90 and 175 PSI, depending on the compressor. You can consult your owner’s manual to find the default cut-out point for your compressor.
Once your compressor reaches the cut-off point, it will stop compressing air. But as you use that air in the compressor, the needle will start to fall back down — until it gets to the cut-in point, at which point the compressor will kick back on to build pressure back up.
The tank gauge doesn’t actually cause the compressor to cut on and cut off. That’s the job of the pressure switch. Instead, the tank gauge simply tells you what the pressure is in the tank, and can tell you if the compressor is kicking on and off at the correct pressure.
Cut-In and Cut-Off Points
The cut-in point is always lower than the cut-out point, and there should always be a minimum differential between the two. What this minimum differential is depends on the device, and can be discovered in the owner’s manual.
Let’s stay there’s a minimum differential of 40 PSI between the cut-in and cut-out points. Adjusting the pressure switch to a differential lower than 40 PSI could end up overworking your compressor because it will turn on and off too quickly. Compressor motors need time to cool down.
Luckily, you can rest assured that the factory settings on your compressor aren’t less than the minimum recommended differential. You really only need to worry about this if you decide to adjust the pressure switch on your compressor.
Regulator Gauge
You can generally tell which gauge is the regulator gauge because it’s located directly under or next to the regulator knob. Whereas the tank gauge tells you how much pressure is in the tank, the regulator gauge tells you how much air pressure is going to the tool or device at the end of the air compressor hose.
This is important because most tools require a certain amount of pressure for proper operation. So if the tool isn’t getting enough air pressure, it may not work well (like a nailer failing to punch a nail all the way into the wood).
If the tool is getting too much pressure, it could cause premature wear on the tool itself. It could also cause other problems. Using the nailer as an example again, too much pressure could cause the nails to go too far into the wood, leaving divots that you may not want.
So you can adjust the regulator knob and watch the pressure change on the regulator gauge, to make sure you’re sending the right amount of pressure to the pneumatic tool.
Tank Pressure vs Regulated Pressure
Tank pressure and regulated pressure are two key stages in the pressurization process of an air compressor. The tank pressure refers to the maximum pressure that can be generated by the compressor, which is typically measured in psi.
The regulated pressure, on the other hand, refers to the pressure of the air that has been regulated by the air regulator before it is released from the compressor. Regulated pressure is typically set to a safe and consistent level that is optimized for the intended use of the compressed air.
To learn about tank pressure vs regulated pressure, it is important to understand the types of gauges commonly used in air compressors. Most air compressors come equipped with two pressure gauges: the tank pressure gauge and the regulator pressure gauge.
The tank pressure gauge displays the pressure level in the air tank, while the regulator pressure gauge displays the regulated pressure level. Spotting irregularities in pressure readings on either gauge can be helpful in troubleshooting issues with the compressor.
When installing a new air compressor or pneumatic tool, it is important to pay attention to the operating pressure and other gauge readings to ensure safe and effective use. Assuming that all gauges and hoses are connected properly, any concerns with pressure regulation or fluctuations can often be resolved by following a few simple steps, such as checking the temperature, oil level, or air filter.
By learning about the key stages of the pressurization process and effectively identifying and addressing any issues that arise, you can ensure that your compressed air products operate smoothly and effectively for years to come.
How To Read An Air Compressor Gauge
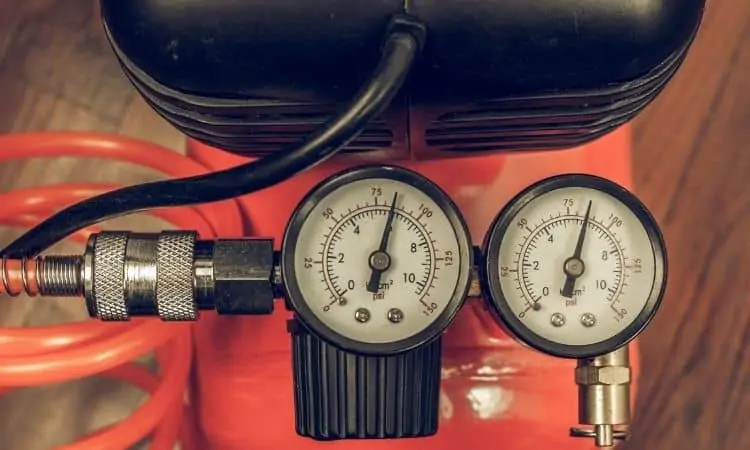
Reading an air pressure gauge is a lot like reading a speedometer on a vehicle. But instead of miles per hour, you’re looking at pounds per square inch (PSI). You can look closely to see how your gauges are divided up and what each small hash mark means.
It’s important to reference your owner’s manual for the correct PSI for a given tool and compare that to the readings on your compressor. This is a lot like referencing the speed limit sign and making sure you’re going around the same speed when you’re driving.
Once you understand how your compressor and the tools you use are supposed to operate, it’s easy to tell if something is wrong with the compressor or the tools. It’s also easy to tell when all is working well since you can read the gauges on your compressor!
How Do Air Compressor Gauges Work?
The needles on the compressor gauges are carefully calibrated during the manufacturing process to respond to internal components that are exposed to the pressure in the tank and/or the air line.
As the pressure builds inside the tank, this causes interaction with the components attached to the gauges, which causes the needle to move correspondingly.
Sometimes the internal components of a gauge can become damaged and need replacing. Luckily, these are cheap to buy and easy to replace.
How To Adjust an Air Compressor Gauge
Some air compressor regulator knobs are locked in place. This is so you don’t accidentally bump the compressor and change the pressure on accident. So if you find that you’re having a hard time adjusting the pressure regulator knob, you may need to pull it out or push it down to unlock it.
Once it is unlocked, you can adjust it to the desired pressure and then push or pull it back into the locked position.
Now all compressor regulator knobs are like this. Some you will be able to adjust without unlocking them, simply by turning them. Your owner’s manual will specify if you do have a compressor with an internal locking component on the regulator knob.
What Do The Gauges Need to Be Set At?
Where you set your regulator gauge depends on the air tool you’ll be using. Most air tools require a PSI of between 70 and 100 PSI. However, it’s important to check your air tool for the proper PSI and CFM. You’ll want to make sure your compressor is capable of operating the tool by consulting the owner’s manual to determine the CFM and PSI the compressor can generate.
It’s important to realize that you can’t use the pressure to regulate more air pressure than the compressor is able to generate. So if you have an air tool that requires a higher PSI than either of your gauges show, you won’t be able to use that air tool with that compressor.
Here are some common air tools and their operating PSI range.
Air Tool | Operating PSI Range |
Tire Inflator | 125 – 150 PSI |
Framing Nailer | 100 – 130 PSI |
Blowgun | 90 – 100 PSI |
Air Hammer | 90 – 100 PSI |
Angle Grinder | 90 – 100 PSI |
Disc Sander | 90 – 100 PSI |
Paint Spray Gun | 90 – 100 PSI |
Speed Saw | 90 – 100 PSI |
Die Grinder | 70 – 90 PSI |
Brad Nailer | 70 – 90 PSI |
Drill | 70 – 90 PSI |
You can also adjust your pressure switch if you need to change the cut-in and cut-out limits. This involves removing the pressure switch housing and adjusting the screws found there. Consult your owner’s manual for details on how to do this safely on your specific compressor.
In Conclusion
The two gauges on your air compressor are important for the proper operation of the compressor itself and the air tools you’ll use with the compressor. The tank gauge tells you how much pressure there is in the tank. The regulator gauge tells you how much pressure is going downstream to the air tool. You can (and should) adjust the regulator gauge to fit the requirements of the tool. Not doing so could cause the tool to malfunction and premature wear.
Reading these gauges is easy once you know what they’re for. And by ensuring the use of tools compatible with your compressor’s capabilities, you’ll be able to enjoy proper tool use and a long life for your compressor.
Tank Pressure vs Regulated Pressure FAQ’s
What is the difference between tank pressure and regulated pressure?
Tank pressure refers to the pressure of the compressed air stored in the air tank of an air compressor. This pressure is the maximum pressure that the compressor can generate, and it is controlled by the compressor pump’s capacity and the tank’s size. Regulated pressure, on the other hand, is the pressure of the air that has been regulated by the air regulator before it is released from the compressor. The air regulator controls the pressure to ensure that the compressed air is released at a safe and consistent pressure level.
What is the pressure range for most air compressors?
The pressure range for most air compressors is between 100 and 150 psi. However, the pressure range can vary depending on the type and model of the compressor. Some compressors have a pressure range of up to 200 psi, while others have a lower range of around 70-90 psi.
Why does the pressure fluctuate in an air compressor?
The pressure can fluctuate in an air compressor due to changes in the demand for compressed air or due to the compressor motor’s speed. When the demand for compressed air increases, the pressure drops, and the compressor pump will kick in to maintain the desired pressure. Similarly, if the motor speed changes, the pressure will fluctuate accordingly. To ensure consistent pressure, most air compressors are equipped with pressure regulators that adjust the pressure as needed.
How do I set the pressure on the air regulator?
To set the pressure on the air regulator, you need to adjust the knob or screw on the regulator until the desired pressure setting is reached. You can do this by turning the adjustment knob clockwise to increase the pressure or counterclockwise to decrease it. You can verify the pressure setting by checking the regulator gauge displays. It is important to set the regulator pressure to the correct level to avoid damage to the compressor and ensure safe operation.
Can I get more compressed air by increasing the tank pressure?
No, increasing the tank pressure does not necessarily mean you will get more compressed air. The amount of compressed air you can get depends on the operating pressure, which is regulated by the air regulator. The air regulator controls the amount of pressure that is released from the tank and adjusts it to a safe and consistent level. Increasing the tank pressure beyond the recommended level can be dangerous and can damage the compressor. It is important to follow the manufacturer’s recommendations for safe operation.