Air compressors can be divided into two broad categories – oil-lubricated and oil-free. Oil-lubricated air compressors have been around longer and tend to be used most in industrial and professional settings. Oil-free compressors, on the other hand, are the type that most people have in their garages or tool sheds. But despite how common they are, there’s still plenty of confusion and debate surrounding oil-free compressors. So in this article, I’ll tell you all the info you need about oil-free air compressors.
Table of Contents
- What Is an Oil-Free Air Compressor?
- How Do Oil-Free Air Compressors Work?
- Do Oil-Free Air Compressors Need Oil?
- How Long Do Oil-Free Air Compressors Last?
- How Much Do Oil-Free Air Compressors Cost?
- How Much Does An Oil-Free Compressor Cost Compared To Oil-Lubed Compressors?
- Are Oil-Free Air Compressors Better?
- Advantages & Disadvantages of Oil-Free Air Compressors
- Our Oil-Free Air Compressor Recommendation
- Oil Free Air Compressor FAQ’s
What Is an Oil-Free Air Compressor?
An oil-free air compressor is an air compressor that doesn’t use oil for lubrication in the pump’s compression mechanism. Instead, the mechanical components are typically coated with a permanent lubricant material such as Teflon. The lack of oil gives these compressors several advantages.
An oil free compressor is generally more portable, less expensive, and easier to maintain than an oil lubricated air compressor, which is why they’ve become the most popular choice for household use and basic contractor work. But they are also used in many factories and industrial settings where a 100% oil-free air supply is a necessity (more on that later).
How Do Oil-Free Air Compressors Work?
An oil free compressor works in the same way as their oil-lubricated counterparts – drawing in air, decreasing its volume, and forcing it into a pressurized storage tank. The difference is that no oil is used in the compression cylinder. Instead, lubrication and cooling are achieved by other means.
There are a few different types of air compressors, each of which uses a different mechanism to compress air. The three main types are piston, rotary screw, and rotary scroll compressors.
Piston Compressors
Reciprocal piston compressors feature a cylinder with a piston inside it. As the piston moves down, a vacuum is created at the top of the cylinder and atmospheric air is drawn into the top of the cylinder through an inlet valve. As the piston moves up, it decreases the volume of the air and simultaneously increases its pressure. At the same time, the now-compressed air is pushed through a discharge valve and into the storage tank.
In an oil-lubed piston compressor, oil is splashed up on the crankshaft, piston arm, and cylinder walls from an oil sump at the bottom of the cylinder, reducing friction and cooling the metal components.
In an oil-free piston compressor, the mechanical components that come in contact with one another are coated in Teflon or a similar material that reduces friction, allowing the mechanism to move freely without oil. These are typically air-cooled by an external fan on the pump housing.
Rotary Screw Compressors
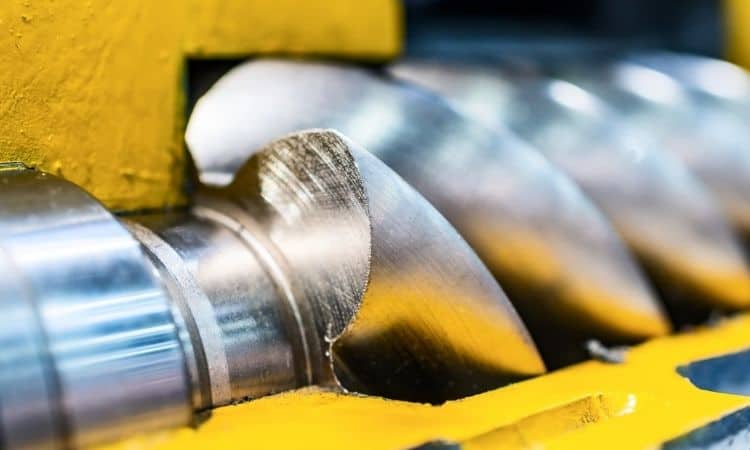
In a rotary screw compressor, the compression chamber features two threaded rotors side-by-side. The threads of each rotor run in opposite directions (often referred to as male and female rotors) so that they rotate in unison, much like gears. However, the rotors are precisely engineered and positioned so that they do not make contact with one another. As air is drawn into the compression chamber, it is forced through the narrow gap between the rotors and is compressed in the process.
In an oil-free rotary screw compressor, there is often oil inside the gearbox that drives the rotors, but this is a separate sealed chamber – no oil can possibly enter the compression chamber (barring some catastrophic damage event).
The rotors themselves require no lubricant since they do not touch, but in some cases, the compression chamber is surrounded by a water coolant system, as the compression process generates heat. In some models, water is injected directly into the compression chamber, but this is less common.
Rotary Scroll Compressors
Scroll compressors feature two spiral-shaped metal pieces inside the compression chamber, one inside the other. As air is drawn into the chamber, the inner spiral oscillates inside the fixed outer spiral, reducing the air’s volume and directing it toward the center of the spiral.
As with a screw compressor, the spiral rotors do not make contact with one another and therefore do not require direct lubrication. Likewise, the sealed gearbox that generates the oscillating rotor movement may contain oil, and the chamber may be wrapped in a water-cooling apparatus, but the compression chamber contains no oil.
Do Oil-Free Air Compressors Need Oil?
Some oil-free air compressors do still need oil for lubrication – the “oil-free” designation simply means that no oil is used in the compression chamber. Oil may still be used inside the gearbox or as a coolant. On some models, you may even need to replace the oil periodically.
On oil-free compressors that does employ oil for the motor or gears, the oil system is designed to be separate from the compression chamber – it is sealed off and self-contained.
Some oil-free models (usually rotary screw compressors) that employ oil in the gearbox require that the oil is changed periodically, but this is usually for larger models.
With an oil-free reciprocating piston compressor (the most common type of compressor), you likely won’t need to worry about oil, as the gearbox and motor are either made with heat-resistant and friction-reducing materials or are lubricated with oil/grease designed to last the lifetime of the compressor.
How Long Do Oil-Free Air Compressors Last?
Oil-free piston air compressors typically last around 10-15 years, while oil-free rotary screw compressors tend to last around 20-30 years. You can generally expect anywhere from 2,000 to 8,000 hours of service. However, the lifespan depends largely on maintenance, proper care, and usage habits.
A common criticism of oil-free compressors is that they don’t have the lifespan of their oil-lubricated counterparts. While this may be true of older models, it’s not exactly fair to say of today’s oil-free compressors. The technology has improved significantly in recent years and only continues to be improved.
That being said, most oil-free compressed air isn’t intended for long-term continuous use applications. In other words, they’re not ideal for running for several hours at a time. The permanent lubrication materials will eventually wear out. So while oil-free compressors may not provide the same number of actual service hours as oil-lubed compressors (typically around 15-20K hours), they will likely last the same number of years, since they’re meant for shorter bursts of service.
How Much Do Oil-Free Air Compressors Cost?
Oil-free air compressors can cost anywhere from $100 to $2,000. Smaller compressors (10 gal. or less) tend to cost $100-$200, mid-size models (20-30 gal.) are in the $400-$600 range, and large ones (60 gal.+) are $1,000-$2,000. Industrial oil-free air compressors go up from there.
How Much Does An Oil-Free Compressor Cost Compared To Oil-Lubed Compressors?
In general, oil-free air compressors for compressed air tend to cost less than oil-lubricated air compressors of comparable size and power. This is mainly due to higher manufacturing and material costs. But even if the up-front price is the same, oil air compressors also come with higher maintenance costs over time.
On an oil-lubed compressor, the oil needs to be regularly topped off and changed, and the oil filter and air/oil separator will need to be replaced periodically. While it won’t exactly be exorbitant, these costs can add up over time, so they’re worth factoring in.
Oil-free compressors, in comparison, require very little maintenance that involves additional purchases – replacing the air intake filter is about the only thing.
Are Oil-Free Air Compressors Better?
Oil-free air compressors are not necessarily better or worse than oil-lubed air compressors. Whether or not it’s right for you mainly depends on what you’ll be using it for. Oil-free compressors may be better suited for certain applications or conditions, but the same can be said of oil compressors.
As we touched on earlier, oil-free air compressors aren’t ideal for continuous-use applications such as cutting, grinding, or painting large surfaces. This is mainly because they are more likely to overheat during long cycles of use, which can prematurely wear out mechanical parts or damage the pump motor.
They also don’t typically have as high of a CFM output as oil-lubed models of the same size, which may limit what kinds of air tools you can use them with. In most cases, they are also a little louder than oil-lubed units.
But oil-free compressors do tend to perform better in cold weather conditions, as they contain no oil (which can get thick or “sludgy” at cold temperatures). They are also easier to transport, as they’re usually made from lighter materials and can be transported in virtually any orientation without fear of oil leaking or fouling internal components.
Naturally, since they neither consume nor burn any oil, they also have less of an environmental impact than oil compressors. Indeed, many models even require less electricity to run than similarly-sized oil compressors.
Another major factor that makes oil-free compressors better for certain applications is that they have virtually no risk of contaminating the compressed air with oil. When oil is used in the compression chamber, a small amount will inevitably make its way into the compressed air supply in the form of vapor. An air/oil separator sits downstream of the discharge valve to prevent it from getting into the tank and/or air lines – but this isn’t always 100% effective.
Even a little oil in the compressed air can destroy a paint job or contaminate breathable air or food/beverages. So depending on what you plan on using your compressor for, an oil-free compressor may be the only way to go.
For a more in-depth comparison, check out my article on Oil vs. Oil-Free Air Compressors.
Advantages & Disadvantages of Oil-Free Air Compressors
To make things easier, here’s a brief breakdown of the key advantages and drawbacks of oil-free air compressors.
Advantages
- Low maintenance
- Generally less expensive than comparable oil-lubed models
- Perform better in cold temperatures
- Virtually no risk of contaminating the air with oil
- Relatively easy to transport
- More environmentally friendly
Disadvantages
- Not ideal for heavy-duty or continuous-use applications
- Lower CFM output than most comparable oil-lubed models
- Shorter lifespan (in terms of service hours)
- Often louder than oil compressors
Our Oil-Free Air Compressor Recommendation
Now that you know all about oil-free compressors, here’s our pick for the best oil-free air compressor on the market today.
This 20-gallon vertical air compressor from the trusted brand Craftsman is a versatile piece of equipment, whether you’re using it for home projects or you’re a contractor who wants a powerful yet portable compressor you can take with you to job sites.
With a 1.8 HP induction motor capable of producing 4 SCFM @ 90 PSI, this compressor boasts rapid recovery times and is powerful enough to run most air tools – even for fairly long bouts of continuous use. The large 20-gallon tank with its 175 PSI maximum pressure rating means longer usage without a lot of waiting.
At just over 3 feet tall with a width of 17” x 23” it’s a fairly compact design, making storage and transportation easy. Weighing in at just under 90 lbs., this is a relatively lightweight compressor for its size. And with two 2” x 8” rubber casters and a convenient handle, it can easily be wheeled around.
The pump housing features two pressure gauges (tank & tool), a regulator knob, and dual quick-connect couplers, so you can run two hoses at once. The tank itself even features a convenient hook for hanging your coiled air hoses.
Bestseller
Features
- 120V 1.8 HP induction motor
- 20 gallon storage tank
- 175 PSI max pressure
- 4 CFM @ 90 PSI, 5 CFM @ 40 PSI
- Two 2” x 8” rubber wheels & a sturdy handle for easy transport
- Dual ¼-inch quick-connect couplers
- 6-foot power cord
- Built-in hook for air hose storage
- 80 dB noise rating
- 50% Duty Cycle
- Comes with 1-year manufacturer’s warranty
Oil Free Air Compressor FAQ’s
What is the difference between oil-free and oil-lubricated compressors?
Oil compressors use oil to lubricate the compressor element, reduce friction, and dissipate heat. The oil is circulated through the compressor, providing a layer of lubrication that helps prevent damage to the compressor element.
In contrast, oil-free compressors do not use oil in the compressor element and rely on alternative means to reduce friction and heat generation. Instead, they use specially designed materials and coatings to reduce wear and tear on the compressor element.
What are the benefits of using an oil-free air compressor?
Oil-free air compressors offer several benefits over oil compressors. Firstly, they provide the highest air purity standards, ensuring that the compressed air is free from oil contamination. This makes them suitable for use in applications where air quality is critical, such as in the food and beverage and pharmaceutical industries.
Secondly, oil-free compressors have reduced maintenance requirements, as there is no need for oil changes or oil filter replacements. Finally, oil-free compressors eliminate the risk of oil contamination in compressed air applications, which can cause damage to equipment and pose safety hazards.
What are the risks associated with using oil-lubricated compressors in compressed air systems?
Oil compressors can pose risks such as oil contamination in the compressed air system. Oil contamination can cause damage to equipment, reduce the quality of compressed air, and create safety hazards in certain applications. In addition, oil injected air compressors require regular oil changes and oil filter replacements to maintain optimal performance, which can add to the maintenance costs.
What is the high-pressure element in an oil-free compressor, and what is its function?
The high-pressure element is a specialized component of an oil-free compressor that compresses pressurized air to the required level. It is designed to handle high pressures and temperatures and maintain the highest air purity standards.
The high-pressure element is responsible for delivering high-quality compressed air to the application, ensuring that the compressed air is free from oil contamination and other impurities.
What is the low-pressure element in an oil-free compressor, and what is its function?
The low-pressure element in an oil-free compressor is responsible for drawing in and compressing the inlet air and transferring it to the high-pressure element. It is designed to minimize compressed air contamination and optimize air quality.
The low-pressure element typically includes an inlet air filter, which removes contaminants from the incoming air and ensures that only clean air is compressed. This helps to maintain the highest compressed air purity standards and ensure that the compressed air is suitable for use in applications where air quality is critical from the oil free air compressors.