An air compressor can be a valuable addition to your arsenal of tools, whether you want it for small tasks like filling tires or heavy-duty work like powering nail guns or painting. But if you’ve never used an air compressor before, it can seem like a pretty intimidating machine. But have no fear – using an air compressor is easier than you think!
In this article, I’ll walk you through every part of the process, from the initial setup to putting it away when you’re done working. I’ll also include a few tips and best practices for keeping your compressor in good shape for the long haul.
Table of Contents
Getting Started
First up, let’s go through setting up your compressor for the first time.
Step 1 – Read the Owner’s Manual
Once you’ve got the compressor out of its packaging, you’ll want to give the user manual a good once-over before doing anything else. While the information in this guide applies to the vast majority of air compressors, it still pays to consult your user manual, as it will contain instructions and warnings regarding your specific model. It will also include some key specifications that will come in handy later.
If for some reason you don’t have the user manual, you should be able to download a copy online by visiting the manufacturer’s website or entering the compressor brand and model number into your preferred search engine (i.e. “craftsdude 1234567 manual”).
Step 2 – Check the Oil (If Applicable)
If you have an oil-lubricated compressor, you’ll first want to make sure it has the right amount of oil in it before attempting to operate it. Most models are sold without any oil in the reservoir, so you’ll have to add it yourself before first use. If you’re using a borrowed or previously-owned compressor, you’ll simply want to ensure the oil is clean and up to the appropriate level.
Check the oil level according to your manual’s instructions (this is typically done either with a dipstick or by examining a small sight glass near the oil fill cap) and add the recommended oil if needed – again, consult the manual for this information.
Step 3 – Position the Compressor
Make sure you put your compressor on a stable, level surface before turning it on. Compressors tend to vibrate quite a bit when they’re running. Smaller models may even move around as a result of this vibration. The last thing you want is for your new compressor to fall off of a workbench or tip over during operation. The best place to put it is on flat, solid ground (such as the concrete floor of your garage).
You’ll also want to put it where it won’t come into contact with moisture, if at all possible. That being said, if you have a gas-powered compressor, do not use it indoors, as it will produce carbon monoxide emissions and harmful exhaust fumes that can be very dangerous in an unventilated space.
Likewise, even with an electric compressor, avoid operating it near other sources of CO emissions, such as wood-burning stoves or vehicle exhaust pipes, as the harmful gas can enter the compressor and contaminate your compressed air supply.
Step 4 – Plug In the Power Cord
Next, you’ll want to plug in your compressor (assuming you’re using an electric model). Make sure the compressor’s power switch is in the “OFF” position before plugging in the power cord. Also, make sure you plug it directly into a grounded 3-prong outlet.
Avoid using power strips or extension cords with your air compressor, as these can throttle the power supply and cause damage to the pump motor. (Consult your user manual to determine if your compressor is compatible with any kind of extension cord – some cords are rated to handle the high power demand of compressor pumps.)
If you need to use your compressor in an area that doesn’t have a suitable outlet, it’s much better to use a longer hose or attach two hoses together.
Step 5 – Connect the Air Hose
To be able to use your compressor, you’ll then need to connect your air hose. Your compressor will have at least one hose connector or “coupler” for this purpose. This coupler is a small metal cylinder with a hole in the end. One end of your air hose will have a “male” plug that fits into this hole.
The outer portion of the coupler is called the collar – notice that you can slide it away from the end with the hole in it and it springs back into place when you let it go. This is the mechanism for locking or releasing the plug.
To connect your hose, simply insert the plug into the coupler until you hear a click. In some cases, you may have to slide back the collar as you insert the plug, then release it once the plug is fully seated. In either case, if you pull on the plug and it doesn’t come out, that means it’s connected.
Some larger compressors have threaded couplers, in which case you’ll have to screw on your hose plug – but these are much less common than the “quick-connect” couplers described above.
Many newer models have two couplers – one that connects directly to the tank and one that connects to the regulator valve, or two that both connect to the regulator. On most compressors, the tank coupler will be next to the tank pressure gauge, while the regulator valve coupler will be next to the regulated pressure gauge. For now, you’ll just want to connect your hose to the regulated coupler.
It’s also worth noting that there are a few different types of plugs and couplers – industrial, automotive, and universal. In most cases, you’ll be dealing with universal couplers and plugs, which work with both of the other types.
Step 6 – Connect Your Air Tool
Once your air hose is hooked up to the compressor, go ahead and attach your desired air tool to the other end of the hose, which will likely have a female quick-connect coupler. As before, simply push the tool’s plug into the coupler until it clicks, then pull on the tool to make sure it’s seated properly.
Whatever tool you use, make sure it’s the appropriate size for your compressor’s CFM (cubic feet per minute) output.
Step 7 – Check the Drain Valve
Before turning the compressor on, it’s a good idea to make sure the tank drain valve is completely closed. This will typically be a small wingnut or valve toggle located on the bottom of the air tank. Check it by hand to make sure it’s closed – you may need to tighten it with a wrench, but avoid over tightening.
Using the Compressor
Now that our compressor is plugged in and ready to go, let’s get to the fun part – operation.
Step 1 – Put On Protective Gear
Before you switch on your compressor and get to work, it’s a good idea to bust out the protective equipment. This means the proper shoes (working with power tools in flip-flops is a recipe for disaster), work goggles/glasses (to protect against flying debris), and earplugs/ear muffs (air compressors can be loud enough to damage your hearing). You may also want to wear gloves, depending on what kind of tools you’ll be using.
Step 2 – Turn On the Compressor
Once you’re all set, flip the power switch to the “ON” or “AUTO” position. The compressor will turn on, making a racket as it does so – that’s normal. As mentioned earlier, it’s also normal for it to move around a little as it vibrates, although this really only happens with smaller models.
As the pump runs, keep an eye on the tank pressure gauge. The needle will rise as the tank fills. When it reaches its maximum PSI level (this figure is usually clearly displayed on the compressor itself), it will trigger the pump’s limit switch, and the pump will automatically turn off.
(Important: If the pump doesn’t turn off when the max pressure is reached and the needle continues to rise above that pressure, immediately turn off the power.)
Step 2a – “Break In” the Compressor
Some compressors require a breaking-in period before they are used. This typically involves running the pump for a certain amount of time (typically anywhere from 10-30 minutes) with the tank drain valve and/or unloader valve left open. This helps ensure that the piston rings are properly seated.
On oil-lubed compressors, it also helps flush out any remnants of the manufacturing process, such as factory oils or metal shavings (you’ll replace the oil immediately after the break-in process).
Consult your user manual to see if your model requires a break-in procedure. If it does, the manual will have specific instructions for how to perform this.
Step 3 – Test the Safety Release Valve
With air in the tank, it’s a good idea to test the safety valve for proper function. This valve – a small, cylindrical metal plug with a little ring attached to one end – will open to release air if the tank pressure gets too high.
To test it, simply pull on the ring, which will pull out the metal valve pin. You should hear a hiss of air escaping. When you stop pulling on the ring, the pin should automatically move back into place, closing the valve. If the valve is stuck or doesn’t move freely, turn off the power and contact the manufacturer about replacing the valve.
(You can do this before the tank is full if you prefer – simply turn the pump off when the tank gauge reads 10 PSI, perform the test, then turn the pump back on.)
Step 4 – Check Your Air Tool’s Pressure Rating
Every air tool has a maximum pressure rating and recommended operating pressure range. You can typically find this information on the tool itself, but if not, consult the user manual that came with the tool. For instance, a tool may have a maximum pressure rating of 120 PSI and an operating range of 75-90 PSI. The important thing is not to pump more pressure into the hose than your tool (or the hose itself) can handle – which brings us to step 5.
Step 5 – Adjust the Pressure Regulator
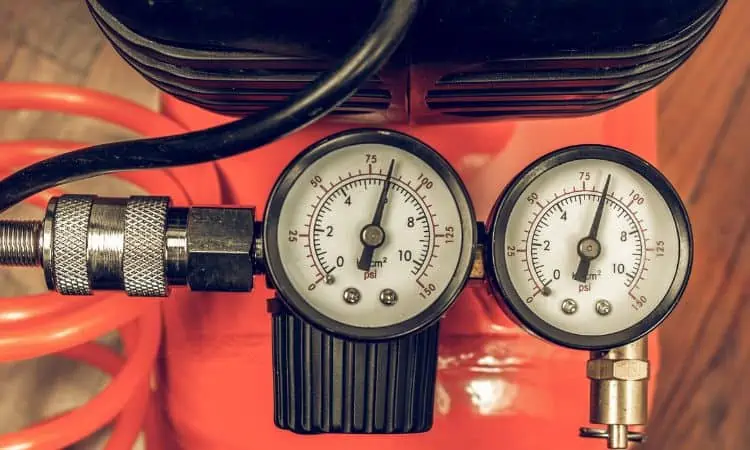
To ensure you’re supplying your air tool with the proper pressure, we’ll look to the regulated pressure gauge (often called the “output pressure” gauge). This will tell you how much pressure is going through the air hose and into your tools.
Near this gauge (typically right between it and the tank pressure gauge) will be a regulator knob. This knob controls the output pressure – turning it to the left (counterclockwise) will give you less pressure, turning it to the right (clockwise) will give you more pressure.
So once you know the proper operating range for your air tool, simply adjust the regulator knob until the regulated pressure gauge shows that pressure. If you turn the knob and the needle doesn’t move at first, don’t fret. You likely just need to use the tool briefly for the gauge to start registering.
Step 6 – Use Your Air Tool(s)
Now you’re ready to start working. As you use the compressed air in the storage tank, the tank pressure will go down. When it reaches a certain point (called cut-in pressure), the pump will kick back on to refill the tank. This is known as “recovery” and will repeat as long as the power toggle is turned on.
If you’re using air faster than your pump can provide it, you may often find yourself waiting for your tank to refill. This is normal – especially for smaller compressors – but you don’t want to overwork your compressor pump or exceed its duty cycle rating, as this can overheat the motor and wear out the pump prematurely. That’s why it pays to do some research and make sure your compressor is well suited to your applications and tools.
During use, if you want to swap out air tools, simply pull back on the coupler collar to release the air tool plug. There will likely be a small burst of air as pressure is released. Then connect the other tool.
After Use
Once you’ve finished using your compressor for the day, it’s time to shut it down and put it away. Here are the steps for doing this properly.
Step 1 – Turn Off and Unplug the Compressor
Turn the power toggle to the “OFF” position and unplug the power cord from the outlet.
Step 2 – Drain the Air
First, turn the pressure regulator knob all the way down. Then, pull the safety valve open to release the tank pressure. Do this until the tank pressure reaches 20-30 PSI.
Step 3 – Drain the Tank of Moisture
Next, open the drain valve on the bottom of the tank to bleed out any condensation that’s accumulated inside the storage tank (condensation forms as the air becomes too compressed to hold it as vapor).
Having a little bit of pressure left in the tank helps blow out the moisture more quickly – just be prepared for this sudden burst of air and water. You can place a shallow drain pan under the valve or simply perform this step in an area where you don’t mind getting a little wet. After this is done, close the valve again. Ideally, this should be performed after every use to prevent rust from developing in your tank.
Step 4 – Disconnect the Air Hose
When the tank is empty, unplug your air hose(s) from the compressor. There may still be a bit of pressure in the hose, so make sure you’re holding it tightly so it can’t whip out at you when you disconnect it from the coupler.
Step 5 – Store Your Compressor
Finally, you’ll want to coil your power cord and air hose neatly and store everything for next time. It’s best to keep your compressor upright in a clean and (relatively) climate-controlled environment. Try to keep it somewhere that won’t be exposed to dust, dirt, or moisture.
Now that you’ve used your compressor for the first time, you’ll just want to keep up with the maintenance. For a complete guide on how to do that, check out my other article here. Thanks for reading!
How To Use An Air Compressor FAQ’s
How do I choose a good air compressor?
When choosing an air compressor, consider the tools you plan to use it with, the size of the job site, and the amount of air pressure recommended for those tools. Also, make sure the compressor’s tank size and pump oil level are suitable for your needs.
What is the difference between gas-powered and electric air compressors?
Gas-powered air compressors are typically more powerful and portable, making them ideal for job sites and outdoor work. Electric air compressors are quieter and more suitable for indoor use.
What is the pressure relief valve on an air compressor, and why is it important?
The pressure relief valve is a safety feature that releases air pressure from the compressor’s tank when it exceeds the recommended level. It is important to prevent accidents caused by escaping air.
How do I maintain my air compressor?
To maintain your air compressor, regularly check the oil reservoir and pump oil level, drain the air tank using the air tank drain valve, and clean the hose line to ensure the air is flowing correctly.